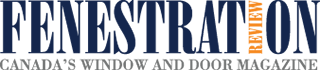
Articles
Dealer’s Corner
Philibuster: The rain up there
Keep an eye on installation details when putting low-rise product into high-rise projects.
April 16, 2025 By Phil Lewin
First off, thanks to George Torok, a senior building science specialist at Stantec, for this topic idea and his copious notes. George thinks it’s high time we had a discussion about putting vinyl window products into high-rise buildings now that code changes have made this more permissible, and I agree.
Traditional low-rise installation has followed a face-sealed approach with fastening through the frame and shims, foam in the rough opening and caulk to the siding. This has been a successful approach for low-rise housing where wind-driven rain loads are low, as long as critical details are addressed.Â
The risk with the face-sealed approach is that the foam in the RO (to be very specific, bead-applied, one-component, polyurethane air sealant foam, complying with the ULC-S710 standard) does not drain. If it gets wet, it stays wet. The wall rots. Mould grows. People get sick. Very expensive repairs are needed.
Taller, more exposed buildings experience higher rain and wind loads. Waterproofing and draining the RO (sub-sill drainage) is essential to protect it, the wall and the interior of the building from wetting and deterioration. Universal application of sub-sill drainage is required by the CSA-A440.6 High Exposure Fenestration Installation standard, which is expected to be included in the 2025 National Building Code. CSA-A440.6 applies to buildings outside the scope of the CSA-A440.4 Window, Door and Skylight Installation standard, which is to say outside of NBC Part 9, so four storeys or more in building height. If it’s not a house or a townhouse, the RO needs to be waterproofed and drained.
So, while it is possible to use low-rise windows in mid-rise buildings, installation details need to evolve from face-seal to drained RO. Window manufacturers need to think differently about the instructions they give to installers to set them up for success. Don’t rely on past, successful experience with houses. It won’t be enough.
Another key consideration with new construction is the distributed nature of installation. In replacement work there is usually only one crew who does everything, including removals, preparing the RO, installation of the product, insulating and air sealing, finishing and sweeping up. In new construction, each of these work items may be done by different trades. There is no one trade for a manufacturer to instruct. An added complication is the trades are expected to follow the installation detailing included in the architect’s drawings and specifications, which are not always specifically suited to the product. The details may be fine for what the architect specified, but what the owner could afford is something else. The exterior look may be the same, the lab-tested wind-driven rain performance meets the specification, but the installation details may not quite work for the purchased product.
Manufacturers and their dealer networks who have done low-rise, new construction work know about some of these issues. Manufacturers and dealers who traditionally have done only replacement work but are moving into new construction are most at risk. It takes more forethought than usual to confirm that product and installation practices are suitable.
One potential problem for manufacturers is the reality that they do not always have access to the details regarding how their products are being used. Distributors and dealers can end up assuming a liability for not having shared project specifications with their manufacturer when products go to projects where they are not appropriately used. When a detailed specification is sent along with a request for quote, manufacturers should have their own engineering staff review the details to avoid a liability for providing inadequate products. Blindly supply product to projects at your company’s peril!
Phil Lewin is technical director of SAWDAC.
Print this page